B3A-1148
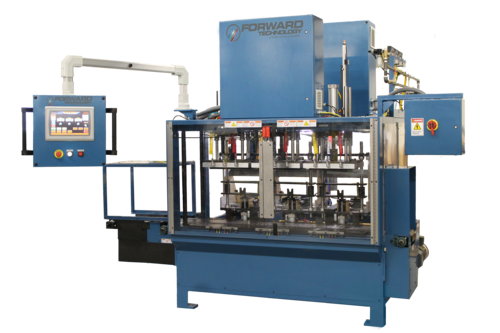
B3A-1148
Horizontal Three Battery Air/Pneumatic Hot Plate Welder
The B3A-1148 is a horizontal heat platen orientation, pneumatic motion controlled hot plate welding system specifically designed for welding: three Standard Group size batteries 9" D x 14" W x 12" H (228mm x 355mm x 305mm) or smaller per welding cycle; OR two Commercial Group size batteries 9" D x 20" W x 12" H (228mm x 508mm x 305mm) or smaller per cycle.
This horizontal systems single motion (upper) tool mounting jaw makes possible automatic feed of the battery components into the equipment for welding and automatic out-feeding of the welded batteries via the system's built-in conveyor system.
The system design is ideal for welding: Battery covers to cases. Battery manifold covers to case covers.

AB PanelView Plus 7 - 1000 Graphic Display Upgrade

Heavy Duty Leveling Casters (Lg.)
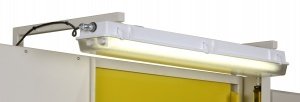
External Lighting (Lg.)
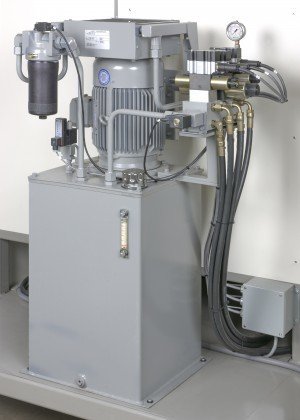
Hydraulic Motion Control
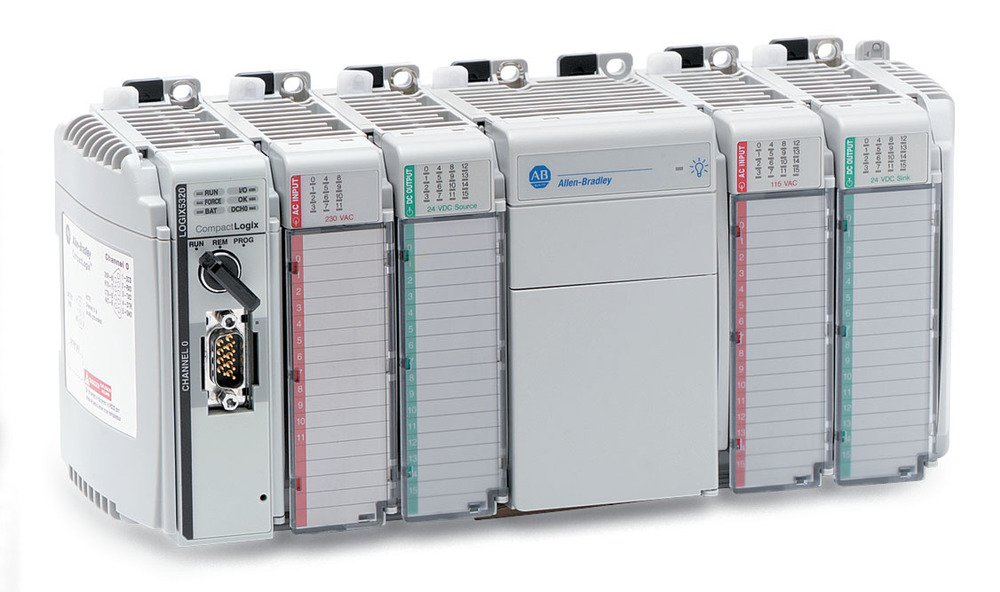
AB Compact Logix PLC Upgrade
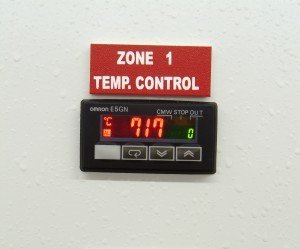
Heat Platen Pre-Heat Controller
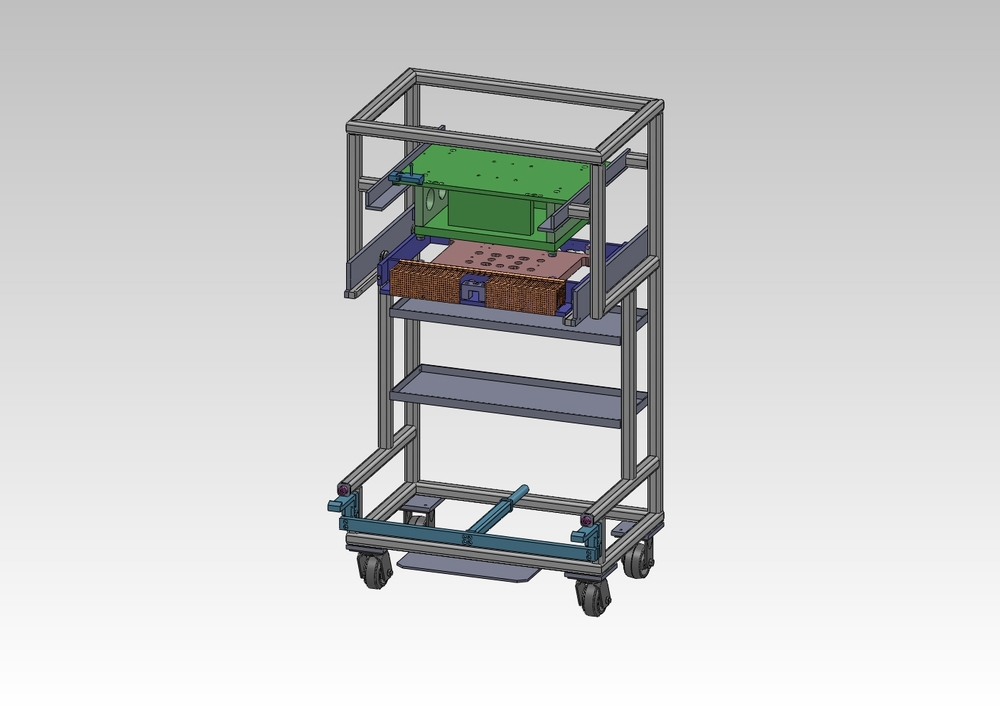
Heat Platen & Tooling/Fixture Storage Cart w/ Casters
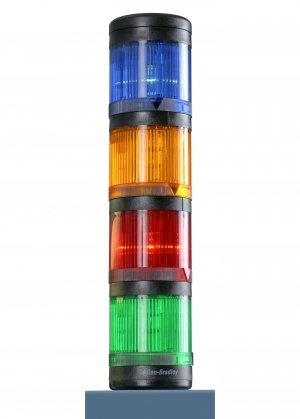
LED Four-Color Light Tower
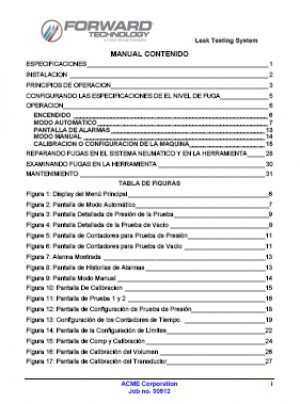
Bilingual Equipment Manual
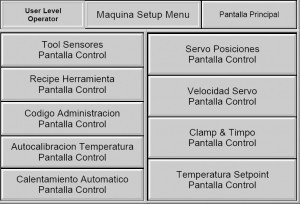
Bilingual User Interface Panel
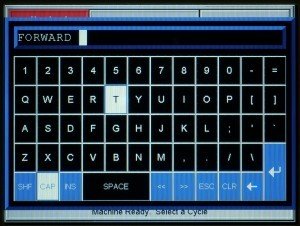
Individual User Passcode Log-In
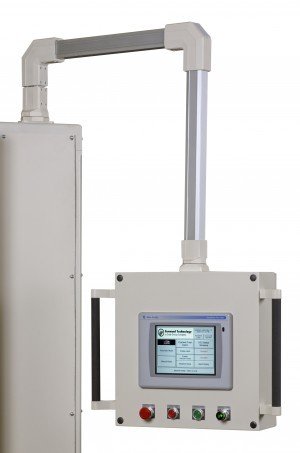
Pendant Arm Mounted User Interface
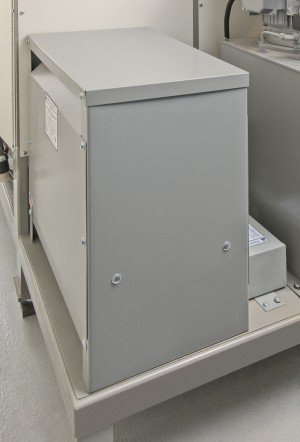
Special Operating Voltages Transformer
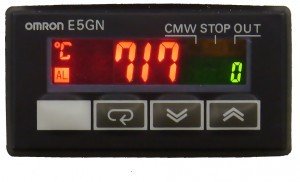
Additional Temperature Control Zone w/ Heater Burnout Alarm
- Pre-assembled un-welded battery covers & cases move down customers assembly line conveyor to the in-feed diverter section of the welders feed-thru conveyor.
- Un-welded battery assemblies are detected via a part presence sensor on the conveyor and are held against a mechanical stop within the in-feed diverter section of the conveyor prior to entry into welding positions.
- When already welded batteries have exited the welding area, the diverter assembly indexes one un-welded battery assembly at a time past the mechanical stop to allow passage of battery down the conveyor to the welding position.
- As battery assemblies move toward the welding area, part presence sensors on the conveyor detect their presence and pneumatically actuated stop blocks hold batteries in the correct position.
- When all batteries have entered the welding area and are detected in correct location by part presence sensors, a pneumatically actuated locator rail bar extends outward to position batteries against an opposing fixed rear rail, squaring them in preparation for welding.
- Conveyor motion stops and welding cycle starts automatically.
- Upper holding fixtures descend downward to pick-up battery covers which are automatically held with vacuum and mechanical grippers. Vacuum Sensors verify a cover was picked-up.
- Upper holding fixtures retract upward with upper battery covers.
- Heat platen advances forward between battery covers and cases.
- Heat platen descends and contacts lower battery cases.
- Upper holding fixtures apply upper battery covers to heat platen.
- Upper holding fixtures retract from heat platen.
- Heat platen rises from lower battery cases and retracts rearward.
- Upper holding fixtures apply upper battery covers & lower battery cases, welding batteries together.
- Upper holding fixtures release clamping mechanisms.
- Upper holding fixtures retract and welded batteries remain atop feed-thru conveyor.
- Pneumatic locator rail and conveyor stop blocks retract and conveyor motion starts.
- Welded batteries are indexed out of machine via feed-thru conveyor.