EH-BT
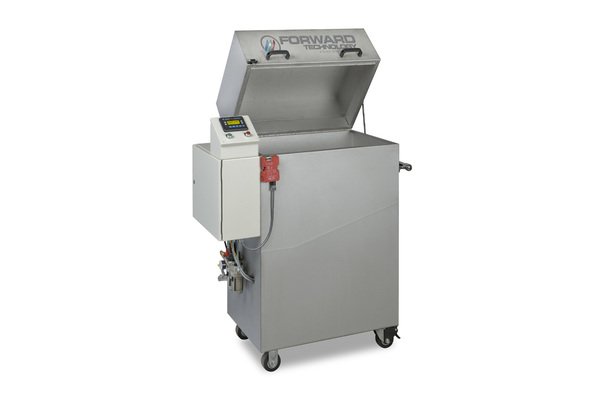
EH-BT
Electronically Controlled Hydraulic Burst Testing System
The EH-BT is an electronically controlled, self contained hydraulic (glycol/water) based burst testing system designed for sample testing applications requiring the highest degree of precision. We offer testers capable of testing fluid pressures up to 750 PSI or 1500 PSI.
The system allows user programmed pressures, ramp rates, and pass/fail limits adjustable digitally in 1.0 PSI increments and has the built-in capacity for cyclical testing if desired.
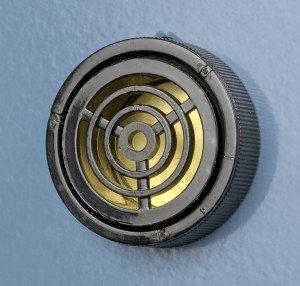
Audible Alarm
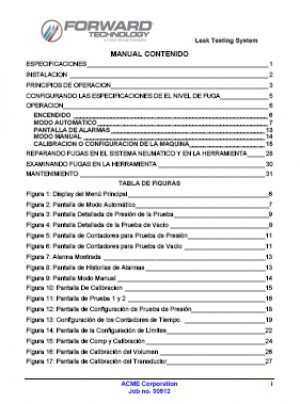
Bilingual Equipment Manual
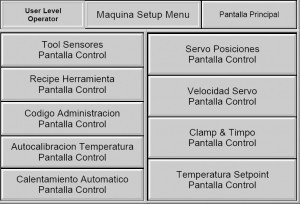
Bilingual User Interface Panel
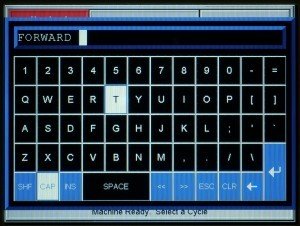
Individual User Passcode Log-In
- Operator loads one part into part chamber.
- Operator manually installs seals/plugs into openings in the test part.
- Operator closes safety cover.
- Safety cover locks.
- Operator actuates cycle activation switch.
- Part is filled with glycol/water mixture, with an appropriate Fill Time to purge all air from the test part.
- Test part is tested in accordance with programming (i.e.: Burst or Cyclic Test).
- Test part ruptures or otherwise satisfies test requirements based on user programmed limits.
- Pressure is released from test part.
- Operator actuates flashing green cycle activation switch and safety cover unlocks.
- Operator removes seals/plugs and connection lines from test part.
- Operator drains residual fluid from test part and removes from test chamber.