HD2X-OSW
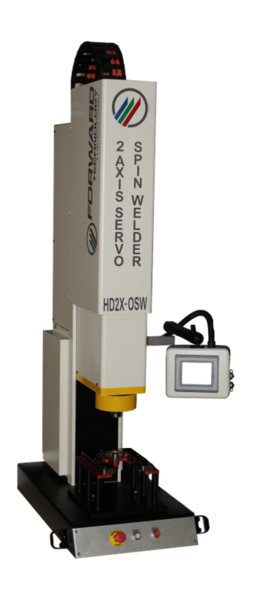
HD2X-OSW
Heavy Duty 2-Axis Servo Electric Orientation Spin Welder
When compared to other orientating or non-orientating models, the HD2X-OSW™ Dual Servo System: Permits precise orientation/alignment of part halves relative to one another (+/- 0.1°). Allows precise control of welding depth (collapse or absolute distance) with an accuracy of (+/- 0.002”). Enables synchronization of vertical and rotational movement to optimize weld process. Provides capability of welding larger parts with more difficult to weld materials (with optional precision gear reducer). Is easier to automate as the spin drivers’ rotational & vertical position may be precisely programmed between welding cycles, decreasing cycle time and allowing automated loading of the upper part half into the spin driver.