Leak Tester
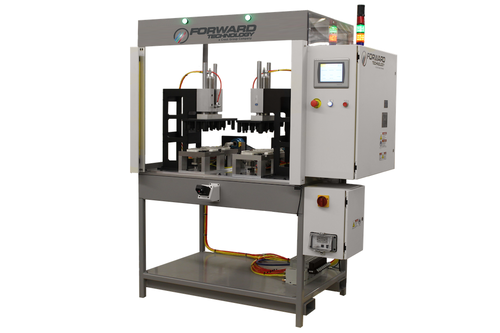
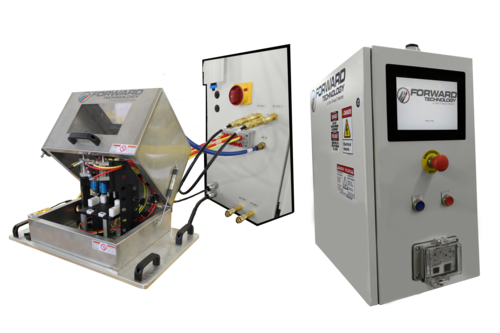
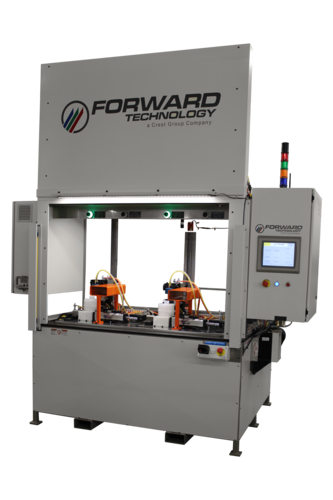
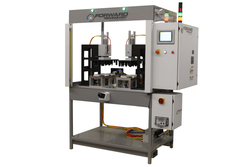

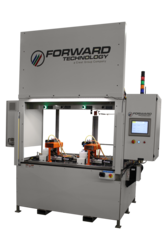
Leak Tester
Leak Testing System
Forward Technology has been integrating leak testing operations into production lines for over 40 years. Testing parts for leakage has become crucial in a number of industries due to safety requirements, quality control issues, and time-saving demands. We know how plastic parts react to leak test operations and our systems combine operator friendliness with detailed process information collection. Our engineers can assist in analyzing your particular leak testing application.
Our PLC based leak testing systems employ a non-destructive test to ensure the integrity of the part. Air testing detects small leaks and eliminates the need for part drying. We offer several air testing methods: Pressure decay Vacuum decay Chamber decay Occlusion testing

AB PanelView Plus 7 - 1000 Graphic Display Upgrade
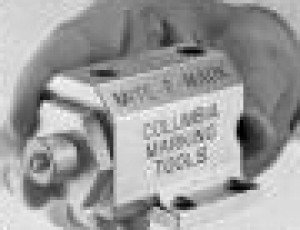
Impact Part Marker
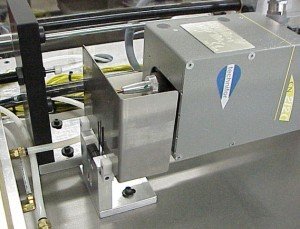
Technifor Part Engraving/Serialization Marker
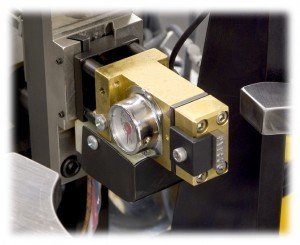
Heated Die Part Marker w/ T-couple Temp. Controller & Heater Burnout Alarm
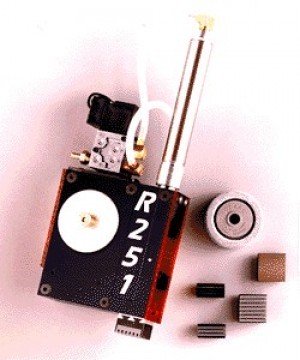
Ink Stamp Part Marker
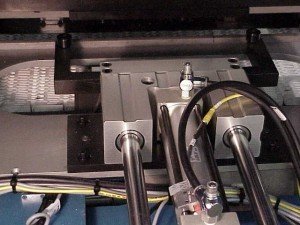
Pneumatically Actuated Electrical Connections
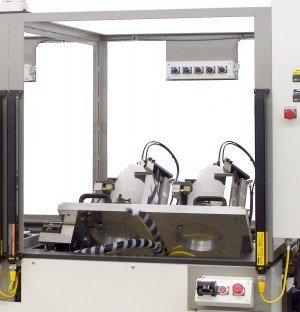
Pivoting Test Fixture
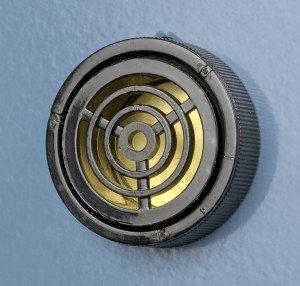
Audible Alarm
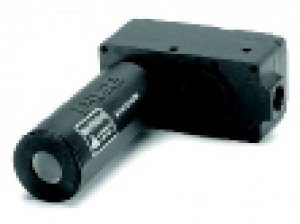
Venturi Vacuum Generator
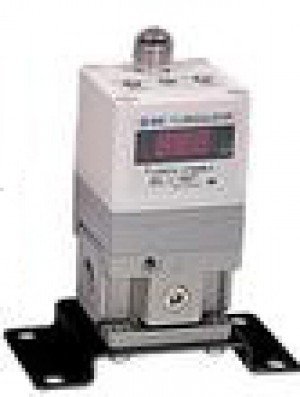
Electronic Regulator
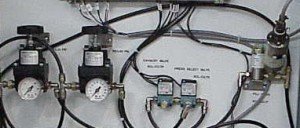
Dual Pressure Option
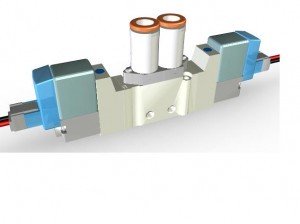
Fixture Clamp Valve
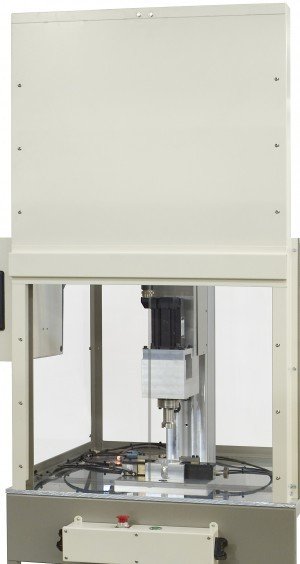
Pneumatic Powered Safety Door
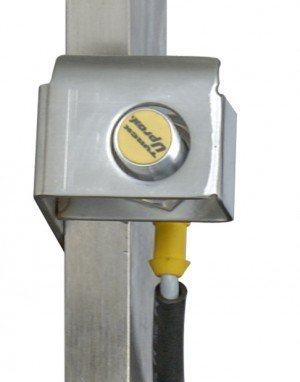
Quick Disconnect Tooling Sensors
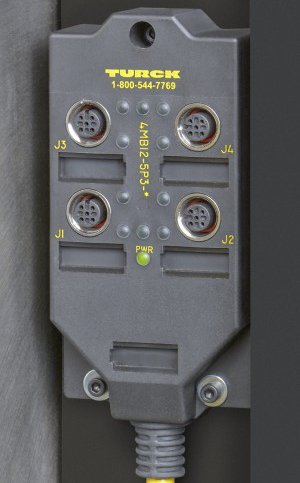
Quick Disconnect Outlets for Tooling Sensors
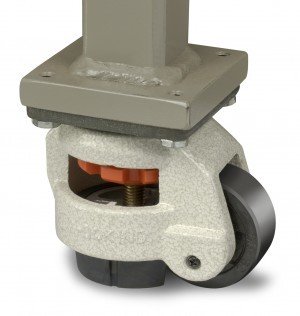
Heavy Duty Leveling Casters (Sm.)
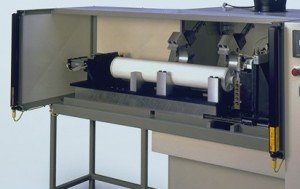
Light Screen Safety Protection (HP)
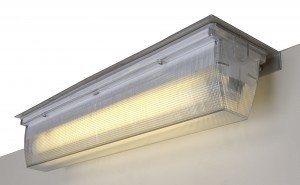
External Lighting (Sm)
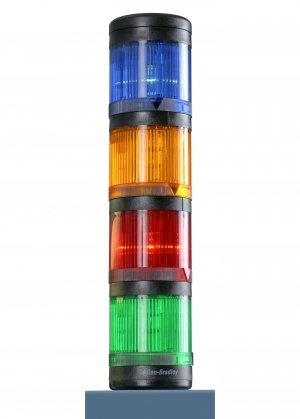
LED Four-Color Light Tower
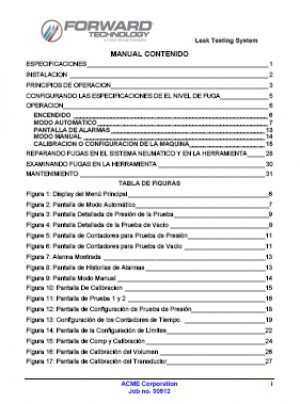
Bilingual Equipment Manual
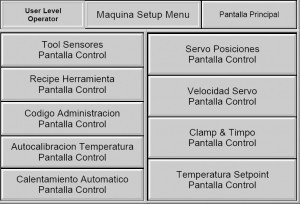
Bilingual User Interface Panel
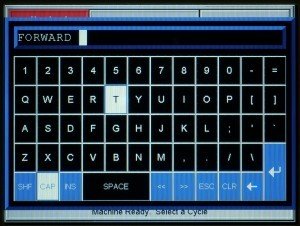
Individual User Passcode Log-In
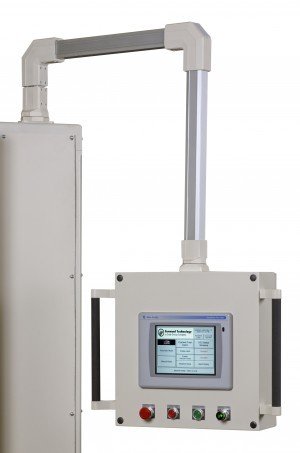
Pendant Arm Mounted User Interface
- Operator loads part(s) to be tested into leak test fixture(s).
- Operator initiates both cycle activation switches.
- Leak test fixture(s) seal heads actuate to seal part(s).
- Operator is permitted to release cycle activation switches after all motions have been completed.
- Leak test analyzer pressurizes part(s) with compressed air.
- Leak test analyzer traps pressure within part(s) and vents pressure supply line to atmosphere.
- Leak test analyzer measures decay of pressure within part(s) and results are compared to user programmed limits.
- If test passes, a green indicator lights and the leak test fixture(s) seal heads retract from part(s), venting pressure to atmosphere.
- If equipped, optional part marker(s) actuate, imprinting character code on passed part(s).
- If test fails, a red indicator lights and the leak test fixture(s) seal heads remain closed, awaiting operator acknowledgment of the failure by again initiating the cycle activation switches.
- If equipped, no optional part marker(s) actuate.
- Operator removes tested part(s) from leak test fixture(s).