VS-1445
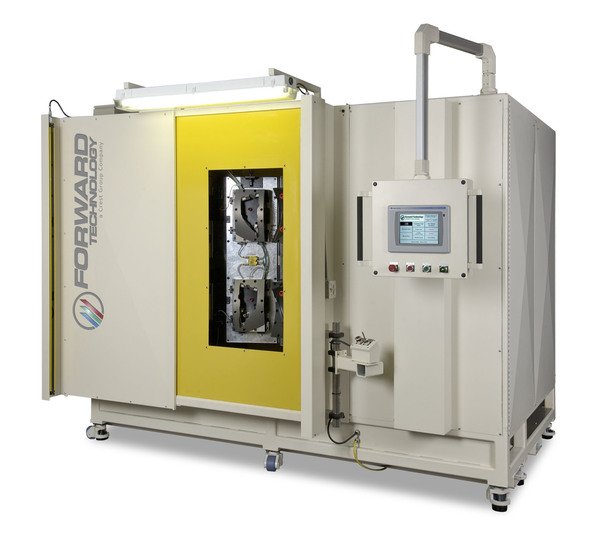
VS-1445
Vertical Servo Hot Plate Welder
The VS-1445 is a vertical heat platen orientation, servo-electric motion controlled hot plate welding system capable of unparalleled control and ultra-precise welding of parts up to 14" x 45" (356mm x 1143mm) or multiple smaller parts. Customized variants of this model are available.
The vertical servo system's twin motion (left and right) tool mounting jaws allow independent control of collapse/absolute distance, time, force & speed on each part half, both when against heat platen in melt phase and against each other in weld phase. Typical hard-stops found in use on most systems are eliminated.
The vertical servo system's twin motion (left and right) tool mounting jaws allow independent control of collapse/absolute distance, time, force & speed on each part half, both when against heat platen in melt phase and against each other in weld phase. Typical hard-stops found in use on most systems are eliminated.
When compared to horizontal platen systems, vertical systems typically: Allow faster tooling changeovers. Allow easier and more positive operator loading and unloading of the tooling. Ensure more precise part half alignment during welding (less scrap) as no special part-part alignment features must be designed into the parts themselves (required for accurate machine pick-up of one part half on horizontal systems).

Heavy Duty Leveling Casters (Lg.)
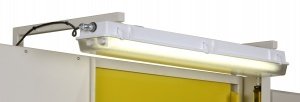
External Lighting (Lg.)
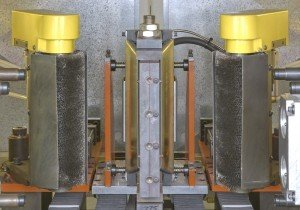
Platen Cleaning Brush System
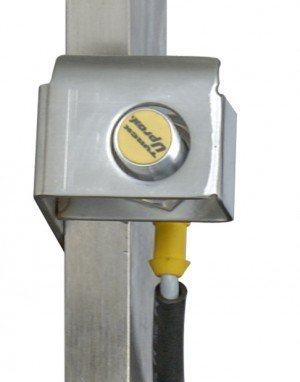
Quick Disconnect Tooling Sensors
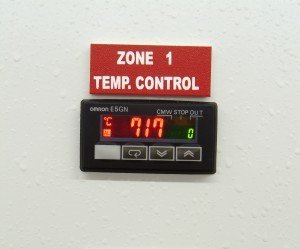
Heat Platen Pre-Heat Controller
Heat Platen & Tooling/Fixture Storage Cart w/ Casters
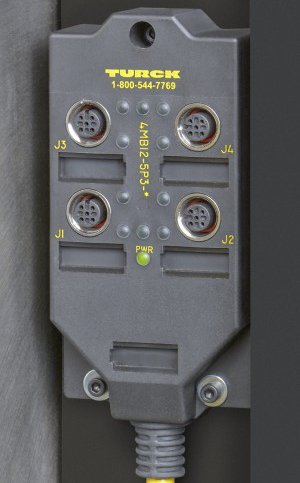
Quick Disconnect Outlets for Tooling Sensors
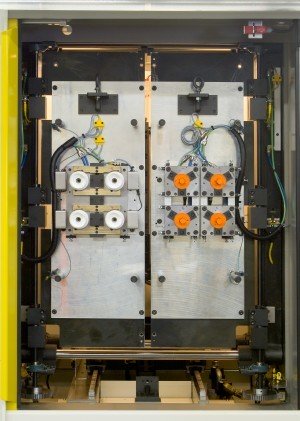
Pivoting Left - Right Tool Mounting Jaws
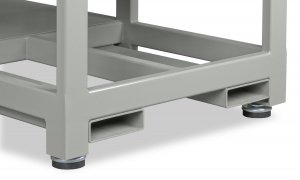
Fork Lift Tubes
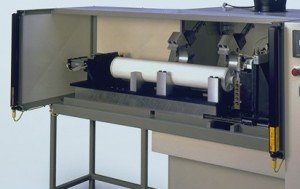
Light Screen Safety Protection (HP)
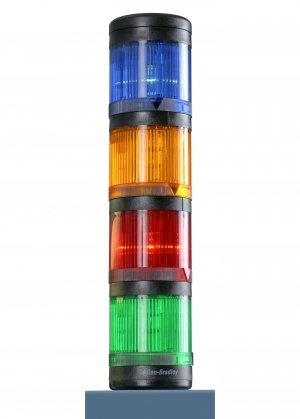
LED Four-Color Light Tower
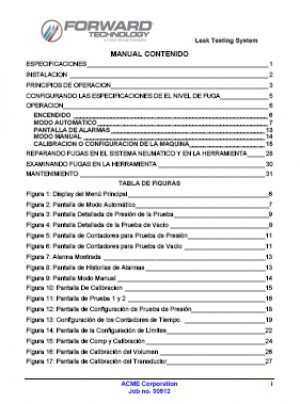
Bilingual Equipment Manual
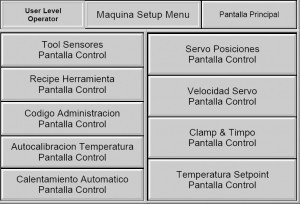
Bilingual User Interface Panel
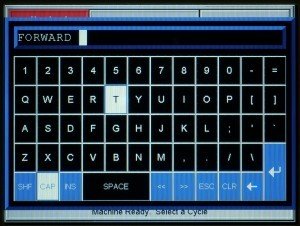
Individual User Passcode Log-In
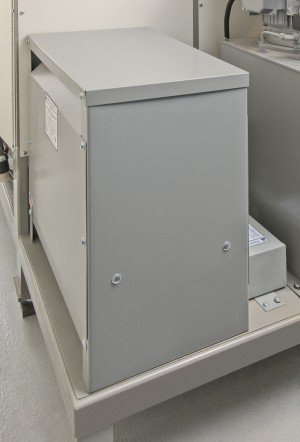
Special Operating Voltages Transformer
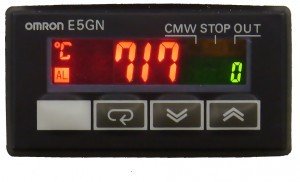
Additional Temperature Control Zone w/ Heater Burnout Alarm
- Operator loads part halves into holding fixtures.
- Operator initiates cycle activation switch.
- Safety door closes.
- Part halves are automatically held with vacuum or mechanical grippers.
- Heat platen advances between part halves.
- Holding fixtures apply part halves to heat platen.
- Holding fixtures retract from heat platen.
- Heat platen retracts.
- Holding fixtures apply part halves together, welding parts together.
- One holding fixture releases its clamping mechanism.
- Holding fixtures retract, retaining welded part(s) in one fixture.
- Safety door opens.
- Operator unloads welded part(s).