VSIR-1445
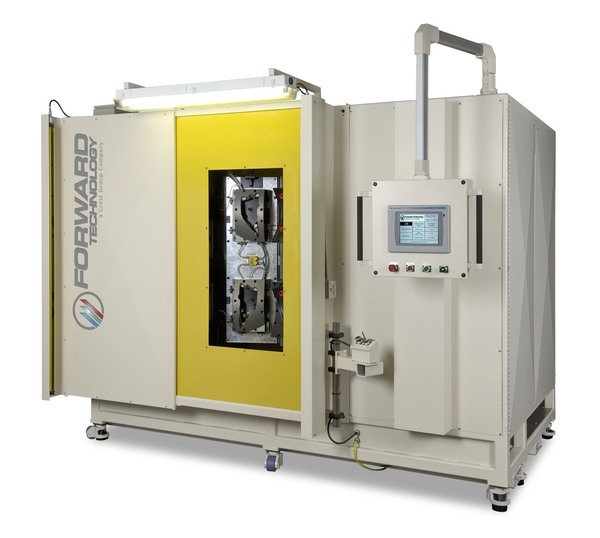
VSIR-1445
Vertical Servo Infrared Welder
The VSIR-1445 is a vertical infrared platen orientation, servo-electric motion controlled infrared welding system capable of unparalleled control and ultra-precise welding of parts up to 14" x 45" (356mm x 1143mm) or multiple smaller parts. Customized variants of this model are available.
The vertical servo systems twin motion (left and right) tool mounting jaws allow independent control of weld (seal), collapse/absolute distance, time, force, & speed on each part half. Typical hard-stops found in use on most systems are eliminated.
The vertical servo systems twin motion (left and right) tool mounting jaws allow independent control of weld (seal), collapse/absolute distance, time, force, & speed on each part half. Typical hard-stops found in use on most systems are eliminated.
When compared to horizontal platen systems, vertical systems typically: Reduce risk of molten material possibly dripping onto the infrared platen during the melt step (resulting in premature emitter failure). Allow faster tooling changeovers. Allow easier and more positive operator loading and unloading of the tooling. Ensure more precise part half alignment during welding (less scrap) as no special part-part alignment features must be designed in the parts themselves (required for accurate machine pick-up of one part half on horizontal systems).
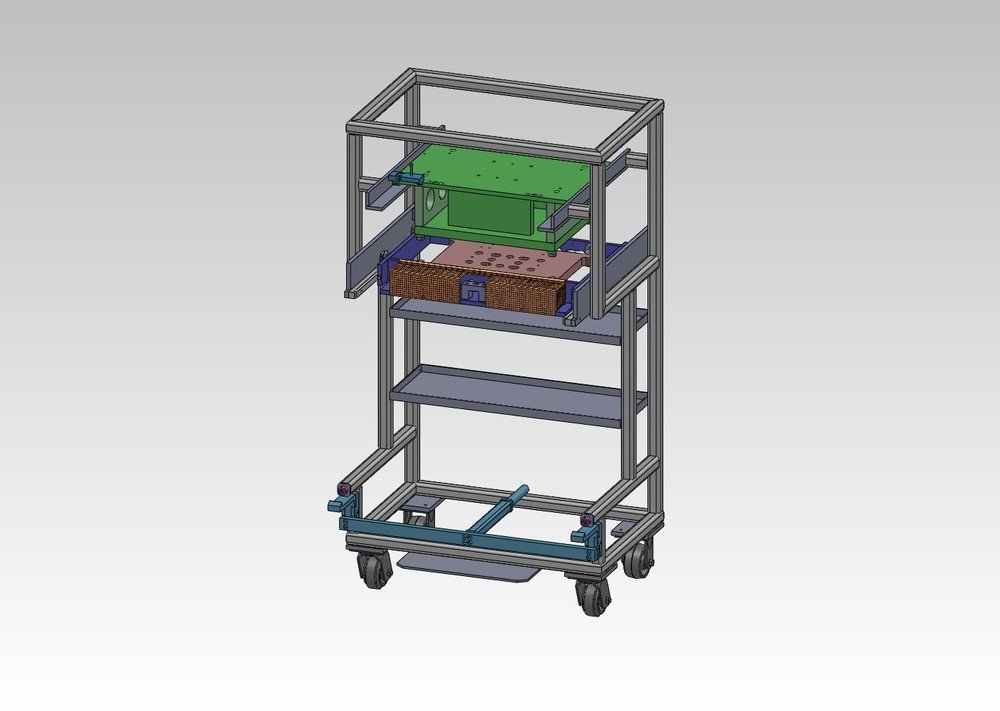
Infrared Tooling/Fixture Storage Cart w/ Casters

Heavy Duty Leveling Casters (Lg.)
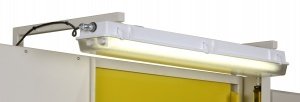
External Lighting (Lg.)
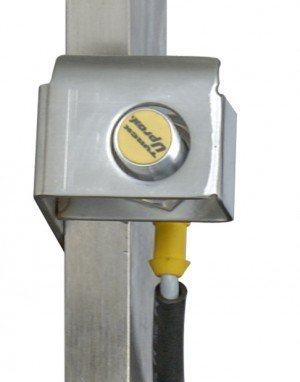
Quick Disconnect Tooling Sensors
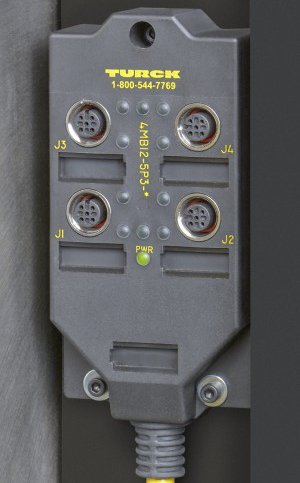
Quick Disconnect Outlets for Tooling Sensors
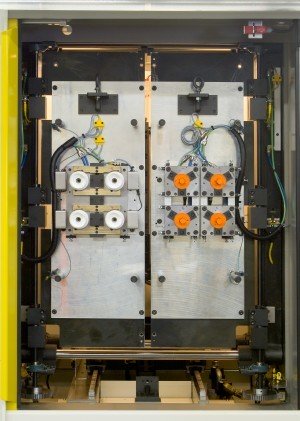
Pivoting Left - Right Tool Mounting Jaws
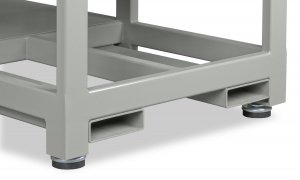
Fork Lift Tubes
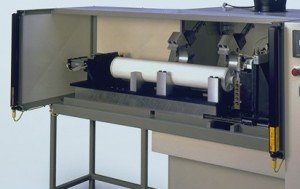
Light Screen Safety Protection (HP)
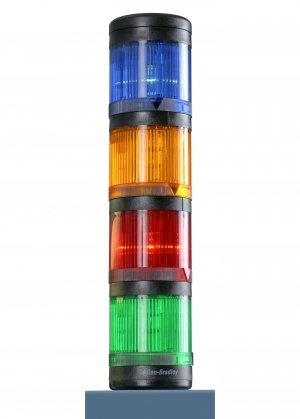
LED Four-Color Light Tower
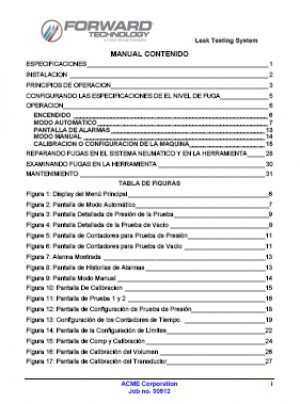
Bilingual Equipment Manual
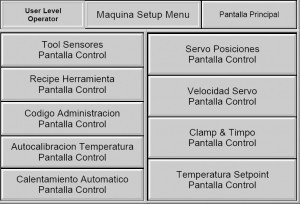
Bilingual User Interface Panel
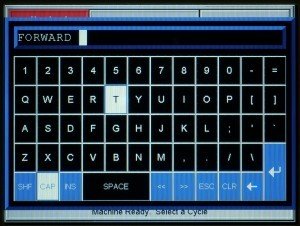
Individual User Passcode Log-In
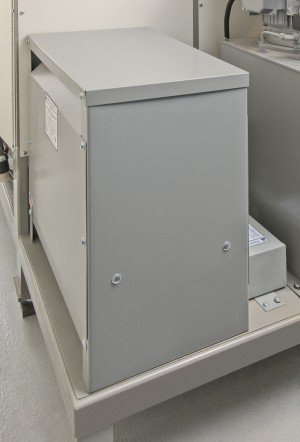
Special Operating Voltages Transformer
- Operator loads part halves into holding fixtures.
- Operator initiates cycle activation switch.
- Safety door closes.
- Part halves are automatically held with vacuum or mechanical grippers.
- Infrared platen advances between part halves.
- Holding fixtures close to precise user programmed proximity from infrared platen to maintain spacing between the parts and the infrared platen without actual contact.
- Infrared platen energizes, heating joint areas of part halves.
- Infrared platen de-energizes and holding fixtures retract away from infrared platen.
- Infrared platen retracts.
- Holding fixtures apply part halves together, welding parts together.
- One holding fixture releases its clamping mechanism.
- Holding fixtures open, retaining welded part(s) in one fixture.
- Safety door opens.
- Operator unloads welded part(s).