Special Spin Welding Systems
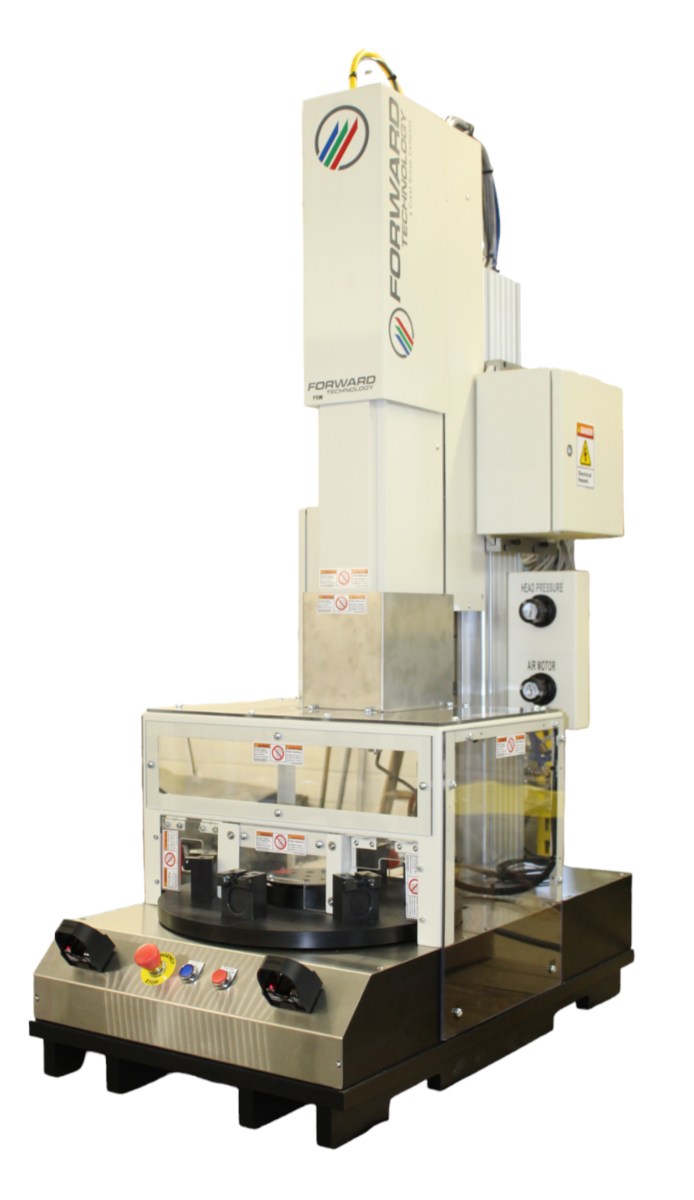
Special Spin Welding Systems
Custom Spin Welder
Forward offers custom spin welding solutions to suit customer's needs. These systems are developed based on customer's input regarding footprint, production requirements, and any other custom features that are required. Common examples of custom spin welding systems include frame based systems, baseless systems meant for automation, or welders designed with an integrated rotary table to ease of operator load and unload without impacting weld cycle time.
These custom spin welders can be designed based from the standard PSW, HD-OSW, or HD2X-OSW models. Custom solutions are our specialty.
When compared to non-custom models, custom spin welding systems allow for end users to fully specify the parameters or design features that best suit their process or product requirements. With Forward's rich experience in designing custom spin welding solutions, chances are that we have an already engineered solution, or close to it, that will suit your needs.
- Operator loads part halves into holding fixture and driver.
- Operator initiates both cycle activation switches.
- Actuator moves driver & rotating part half (typically without rotation) into contact with the stationary fixtured part half.
- Operator is permitted to release cycle activation switches after part to part contact is made.
- Servo motor spins parts at user-programmed RPM for the number of user-programmed revolutions (or user-programmed: time, collapse distance, or absolute distance) and terminates rotation when desired weld criteria is reached.
- Welded parts cool under pressure.
- Actuator retracts to home position and servo slowly rotates to user-programmed home position.
- Operator removes welded part from fixture.